进阶篇:3.1.1)DFM-注塑件设计
本章目的:设计符合塑料模塑工艺(即注塑)的零件,不再犯简单错误,不必再为反复修改模具而烦恼。
1.基础阅读
2.注射成型(Injection Molding)工艺
注射成型(Injection Molding),简称注塑,是一种通过将材料注射到模具中制造零件的制造方法。是塑胶加工工艺的一种。
在这个过程中,塑料被放置到料斗,然后料斗将塑料加热注入,它是通过一长的腔室与一个往复螺杆推压。之后,它被软化成流体状态。喷嘴位于腔室的末端,流体塑料通过喷嘴强制冷却,闭合模具。当塑料冷却和固化时,半成品从压机中退出。
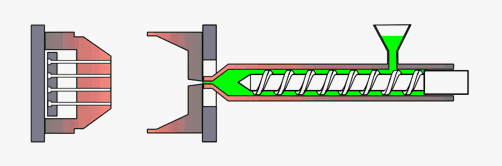
3.DFM注塑件设计指南
本节就开始介绍设计注塑件需要注意的设计指南。
3.1 注塑模具可行性设计
产品设计需要考虑注射模具结构的可行性和提高模具的使用寿命。
3.1.1 理解注塑的原理,设计符合注塑工艺的零件
作者反复思量之后,可能对于新手或行业外的人,这一条反而是最先需要解释的。如果以前是只接触金属加工工艺的人,就需要特意去理解一下,什么是注塑了:如上面的2小节的图所示。不能用做机械加工的思路去做塑胶件,也不要去故意挑战注塑工艺的极限,去搞专门做不出来的零件。
如下图所示:
也许有些人会认为这是一种创新,会强行要求供应商制造。但你出得起这种工艺的钱,别人也行,分分钟会被其他的对手抄袭,比较得不偿失的。
3.1.2卡扣等结构应为斜销(或滑块)预留足够的退出空间
卡扣等结构是塑胶件常用的一种装配方式,通过模具中的斜销(或滑块)侧向抽芯结构成型而成。斜销(或滑块)在零件脱模时有一个从卡扣中退出的行程,零件的设计需要为斜销(或滑块)的退出提够足够的运动空间,否则会出现斜销(或滑块)无法退出或者斜销(或滑块)在退出过程中与零件上其他特征(如支柱等)发生干涉的现象,如图3-71所示。
3.1.3 避免模具出现薄铁以及强度太低的设计
在塑胶件中,如果两个特征距离非常近,那么在模具上相对应的部位就是一块薄铁,如图3-72所示,这容易造成模具强度低、寿命短,因此需要避免在模具上出现薄铁以及强度太低的设计。
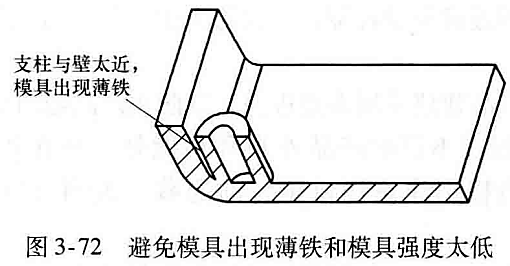
3.2 零件壁厚
在塑胶件的设计中,零件壁厚是首先要考虑的参数,零件壁厚决定了零件的力学性能、零件的外观、零件的可注射性以及零件的成本等。可以说,零件壁厚的选择和设计决定了零件设计的成功与失败。
3.2.1 零件壁厚必须适中
由于塑胶材料的特性和注射工艺的特殊性,塑胶件的壁厚必须在一个合适的范围内,不能太薄,也不能太厚。
壁厚太薄,零件注射时流动阻力大,塑胶熔料很难充满整个型腔,不得不通过性能更高的注射设备来获得更高的充填速度和注射压力。
壁厚太厚,零件冷却时间增加(据统计,零件壁厚增加1倍,冷却时间增加4倍),零件成型周期增加,零件生产效率低;同时过厚的壁厚很容易造成零件产生缩水、气孔、翘曲等质量问题。
不同的塑胶材料对塑胶件的合适壁厚有不同的要求,甚至不同塑胶材料生产商生产的同一种塑胶材料也可能存在不同合适壁厚要求。常用塑胶材料零件的合适壁厚范围见表3-7。当塑胶件壁厚值接近表中的合适壁厚值的上下限时,产品设计工程师应当向塑胶材料生产商征求意见。
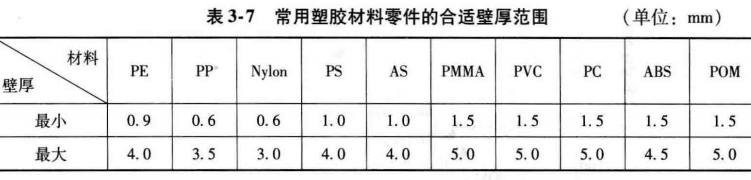
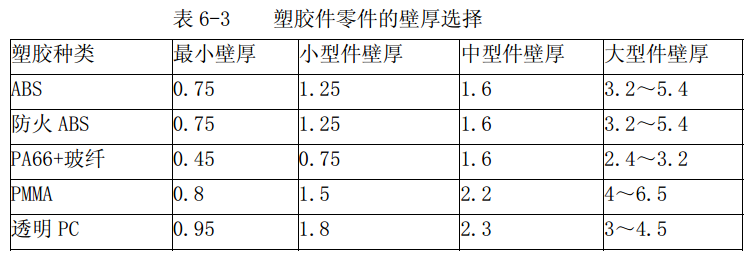
3.2.2 尽量减少零件壁厚
决定塑胶件壁厚的关键因素包括:
1)零件的结构强度是否足够。一般来说,壁厚越厚,零件强度越好。但零件壁厚超过一定范围时,由于缩水和气孔等质量问题的产生,增加零件壁厚反而会降低零件强度。
2)零件成型时能否抵抗脱模力。零件太薄,容易因顶出而变形。
3)能否抵抗装配时的紧固力。
4)有金属嵌件时,嵌件周围强度是否足够。一般金属嵌件与周围塑胶材料收缩不均匀,容易产生应力集中,强度低。
5)零件能否均匀分散所承受的冲击力。
6)孔的强度是否足够,孔的强度容易因为熔接痕影响而降低。
7)在满足以上要求的前提下,而且注射成型不会产生质量问题,塑胶件零件
壁厚应尽量做到最小,因为较厚的零件壁厚不但会增加材料成本、增加零件重量,同时会延长零件成型的周期,从而增加生产成本。图3-19所示为某款ABS塑料零件壁厚与冷却时间的关系。
为了保证和提高零件强度,产品设计工程师往往倾向于选择较厚的零件壁厚。
事实上,通过选择较厚零件壁厚来保证和提高零件强度不是最好的方法。零件强度的提高可以通过添加加强筋、设计曲线或波浪形的零件剖面等来获得,这不但可以减少零件的材料浪费,也缩短了零件注射成型的周期。
3.2.3 零件壁厚均匀
最理想的零件壁厚分布是在零件的任一截面上零件厚度均匀一致。不均匀的零件壁厚会引起零件不均匀的冷却和收缩,从而造成零件表面缩水、内部产生气孔、件翘曲变形、尺寸精度很难保证等缺陷。
常见塑胶件均匀壁厚设计的范例如图3-20所示。
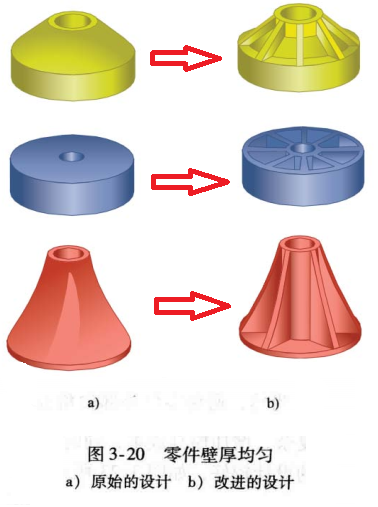
如果零件均匀壁厚不可能获得,那么至少需要保证零件壁厚处与壁薄处有光滑的过渡,避免零件壁厚岀现急剧的变化。急剧变化的零件壁厚影响塑胶熔料的流动,容易在塑胶背面产生应力痕,影响产品外观;同时易导致应力集中,降低塑胶件的强度,使得零件很难承受载荷或外部冲击。
四种零件壁厚不均匀处的壁厚设计如图3-21所示。
最差的壁厚设计见图3-21a,零件壁厚出现急剧变化;
较好的壁厚设计见图3-21b和3-21c,壁厚壁薄处均匀过渡,一般来说,过渡区域的长度为厚度的3倍;
最好的壁厚设计见图3-21d,不但零件壁厚光滑过渡,而且在零件壁厚处使用了掏空的设计,既可以保证零件不发生缩水,又可以保证零件强度。
3.2.4 软件壁厚分析功能
关于塑胶件的壁厚,可以用软件的壁厚分析功能查看,更加直观清晰。

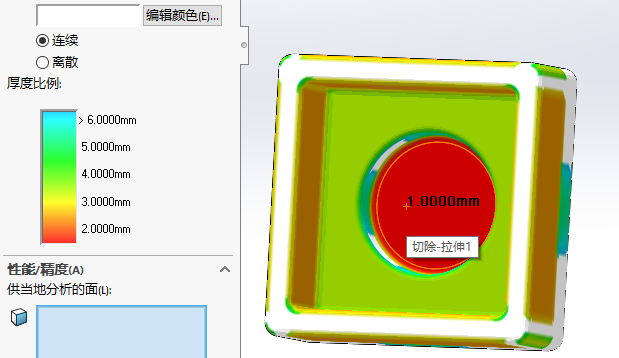
3.3 避免尖角
塑胶件的内部和外部需要避免产生尖角,尖角会阻碍塑胶熔料的流动,容易产生外观缺陷;同时在尖角处容易产生应力集中,降低零件强度,使得零件在承受载荷时失效。因此,在塑胶件的尖角处,应当添加圆角,使得零件光滑过渡。
//因此,结构工程师在3d模型上应该尽量加上圆角。塑胶件开模时用的是3d图。
3.3.1 避免在零件外部尖角(分模线处例外)
塑胶件外部圆角设计如图3-22所示。
当然,避免零件外部尖角也不可一概而论。零件分型面处的圆角会造成模具结构复杂,增加模具成本,同时零件上容易出现断差,影响外观。在零件分型面处直角的设计较好,如图3-23所示。
如果在连接处增加一段约1.5m的平面,在飞边和浇口的去除过程中,飞边和浇口很容易被去除,如图5-18所示。(注塑件一般不用这么注意)
3.3.2 避免在塑胶熔料流动方向上产生尖角
在塑胶件塑胶熔料流动方向上避免产生尖角,如图3-24所示,图中箭头的方向为塑胶熔料的流动方向。在原始的设计中,尖角易导致零件在注射过程中产生困气,局部的高温造成塑胶分解,在零件表面产生外观缺陷,同时尖角容易产生内应力;在改进的设计中,通过设计的优化避免尖角的产生,保证塑胶熔料的流动顺畅。
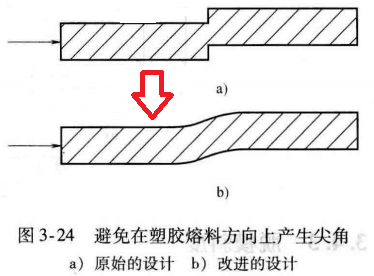
3.3.3 避免在壁连接处产生尖角(内圆角0.3T<R<0.8T,一般0.5T)
应力集中是塑胶件失效的主要原因之一,应力集中降低了零件的强度,使得零件很容易在冲击载荷和疲劳载荷作用下失效。
应力集中大多发生在零件尖角处。塑胶件应当避免尖角的设计,在尖角的地方添加圆角,以减小和避免应力集中的发生。零件尖角容易出现在零件主壁与侧壁连接处、壁与加强筋连接处、壁与支柱连接处等。
零件内部圆角与应力集中系数的关系如图3-25所示。其中T为零件壁厚,R为零件内圆角,p为零件承受的载荷。
由图3-25可见,当R<0.3T时,应力急剧升高;当R>0.8T时,则基本没有应力集中现象发生。
一般来说,零件截面连接处内部圆角R为0.5T,外部圆角为1.5T,既保证了零件的均匀壁厚,又减少了零件连接处应力集中,如图3-26所示。当然,圆角也不可太大,否则容易使得零件局部壁 厚太厚,造成缩水。
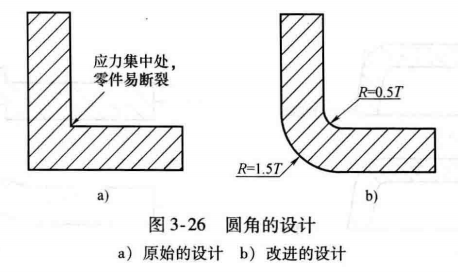
3.3.4 注塑件圆角也是对模具电极的一种保护
在模具加工中,放电加工是一种常用的加工方式,特别是针对复杂曲面。在这种加工方式中,就需要用到电极。
电极的尖角、棱边等凸起部位,在放电加工中比平坦部位损耗要快。
所以一些有担当的模具工程师,反而会要求零件设计有圆角,不然自己也会给塑胶模具加上最小的0.2的圆角。
作者和一位模具工程师的关于圆角的聊天情况如下(目的是为了确认模型的所有边是否要打上圆角);
3.3.5 建模中打圆角的步骤
这只是作者的总结和建议。
塑胶圆角的建模处理并非一次性就可以成功的,建议遵守以下要求。
3.3.5.1 建模最后的步骤才打圆角
可见国标GB26099的规范,圆角建模如下图:
3.3.5.2 塑胶零件模型所有的边都打上圆角,一般第一次打圆角建议值为R0.5
如上述的避免尖角的要求,既然外部尖角、流动方向、连接处都希望有圆角,那么就等于整个塑胶模型都需要圆角。所以作者建议,塑胶模型所有的边全部打上圆角。分型线的圆角可以让模具工程师后期删除。
打圆角步骤:一般先用边圆角打重要的边,再打不重要的边,最后用面圆角打剩余的边。面圆角少用,因为不容易控制和修改。
圆角可以用边圆角分类多打几次,不要一次性打完所有圆角,这样也不容易控制和修改。
3.3.5.3 按照-避免尖角--的原则,修改圆角值,达到最优化的要求
当然,一些特殊的,一眼可见的圆角可以直接打R1等值。
3.4 加强肋的设计
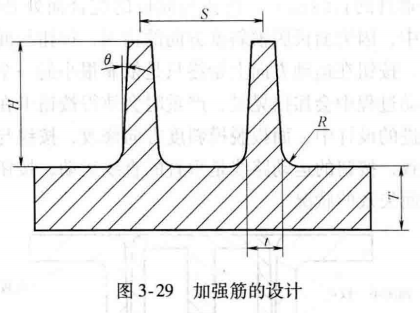
3.4.1 加强筋的厚度不应该超过塑胶零件厚度的50%~60%
对于薄壁塑胶件(零件厚度小于1.5mm),加强筋的厚度可以超过表中比值、甚至等于零件壁厚。加强筋厚度越薄,表面缩水程度越小。
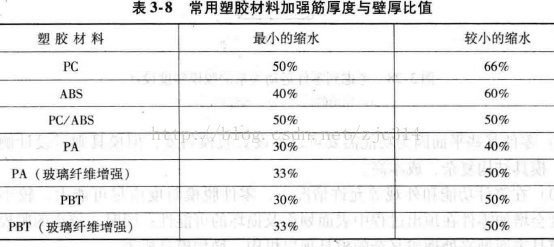
3.4.2 加强筋的高度不能超过塑胶零件厚度的3倍
为了提高零件的强度,加强筋的高度越高越好。但加强筋的高度太高,零件注射闲难,很难充满,特別是当加强筋增加脱模斜度后,加强筋的顶部尺寸变得很小时。加强筋的高度一般不超过塑胶件壁厚的3倍,即H≤3T。
3.4.3 加强筋根部圆角为塑胶零件厚度的0.25~0.5倍
如上一节所述,加强筋的根部需要增加圆角避免应力集中以及增加塑胶熔料流动性,圆角的大小一般为零件壁厚的0.25~0.50倍,即R=0.25T~0.50T。
3.4.4 加强筋的脱模斜度一般为0.5°~1.5°
为了保证加强筋能从模具中顺利脱出,加强筋需要一定的脱模斜度,一般为0.5°~1.5°,斜度太小,加强筋脱模困难,脱模时容易变形或刮伤;斜度太大,加强筋的顶部尺寸太小,注射困难,强度低。
3.4.5 加强筋与加强筋之间的距离至少为塑胶零件厚度的2倍
加强筋与加强筋之间的间距至少为塑胶件壁厚的2倍,以保证加强筋的充分冷却,即S≥2T。
3.4.6 加强筋的设计需要遵守均匀壁厚原则
加强筋设计需要遵守均匀壁厚原则。加强筋与加强筋连接处、加强筋与零件壁连接处添加圆角后,很容易造成零件壁厚局部过厚。
如图3-30所示,加强筋与加强筋连接处增加圆角后会造零件壁厚局部过厚,容易造成零件表面缩水。此时可在局部壁厚处做挖空处理,保持零件均匀壁厚,避免零件表面缩水的发生。
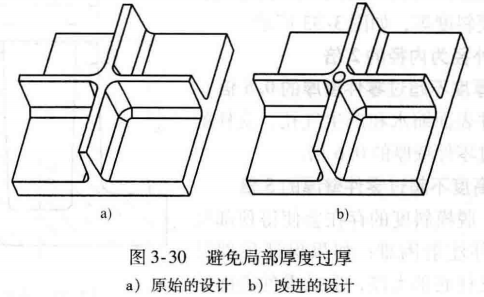
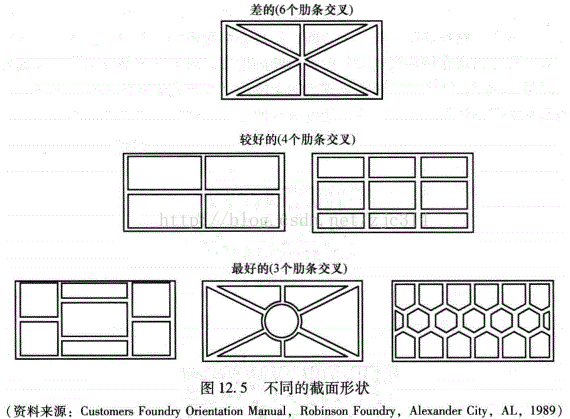
3.4.7 加强筋的顶端增加斜角避免困气
加强筋顶端应避免直角的设计,在注射过程中,直角的设计很容易造成顶端困气,带来注射困难和产生注射缺陷。如图3-31所示,可以在加强筋顶端增加斜角或圆角避免零件困气问题的产生。
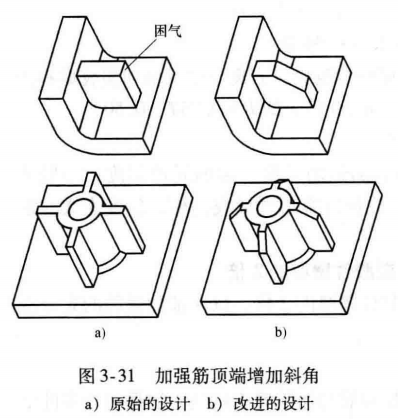
3.4.8 加强筋的方向与塑胶溶料的流向一致
加强筋方向应与塑胶熔料流动方向一致,确保熔料的流动顺畅,提髙注射效率,避免产生困气等注射缺陷,如图3-32所示。
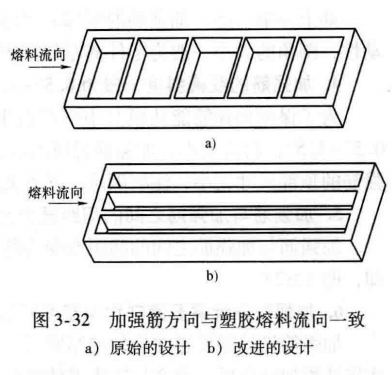
3.5 支柱的设计

3.5.1 支柱的外径为内径的2倍
3.5.2 支柱的厚度不超过零件厚度的0.6倍
为避免零件表面缩水和产生气孔,支柱的厚度不应该超过零件壁厚的0.6倍。
3.5.3 支柱的高度不超过零件厚度的5倍
支柱太高,脱模斜度的存在会使得顶部尺寸小,导致零件注射困难;如果保证顶部尺寸,又会造成支柱底部太厚,造成零件表面缩水和产生气孔。因此,支柱的高度一般不超过零件壁厚的5倍,即h≤5T。
3.5.4 支柱的根部圆角为零件壁厚的0.25~0.5倍
如上一节所述,为了避免零件应力集中和使得塑胶熔料的流动顺畅,支柱的根部圆角为零件壁厚的0.25~0.50倍,即R=0.25T~0.50T。
3.5.5 支柱根部厚度为零件壁厚的0.7倍
为避免外观表面缩水缺陷的产生,支柱的根部厚度可设计为不大于零件壁厚的0.7倍,即t≤0.7T。
3.5.6 支柱的脱模斜度(一般内径0.25°,外径0.5°)
一般来说,支柱内径的脱模斜度为0.25°,外径的脱模斜度为0.50°。但支柱也可以不用脱模斜度,在模具中使用套筒来脱模,但模具费用稍髙。
3.5.7 保证支柱与零件壁连接
避免孤零零的支柱设计,通过加强筋把支柱与零件壁连接成一个整体,增加支柱的强度,并使得塑胶熔料的流动更加顺畅,如图3-34所示。
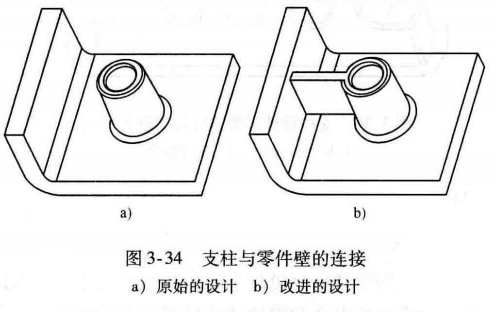
3.5.8 单独的支柱四周增加加强筋补强
当支柱远离浇口时,在支柱上很容易产生熔接痕,熔接痕会降低支柱的强度。当支柱是自攻螺钉支柱时,由于强度不足,支柱常常会在径向力作用下而发生破裂,对固定金属嵌件的支柱也是如此。因此,需要在单独的支柱四周添加加强筋,增加支柱的强度,同时在加强筋与支柱的连接处添加一定的圆角。
单独支柱的加强筋补强设计如图3-35所示。
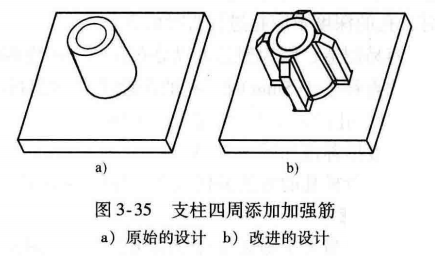
3.5.9 支柱的设计需要遵守均匀壁厚原则
避免支柱过于靠近零件壁。当支柱过于靠近零件壁时,容易造成局部壁厚过厚,导致零件表面缩水和产生气泡。支柱设计应当遵守均匀壁厚原则,如图3-36所示。
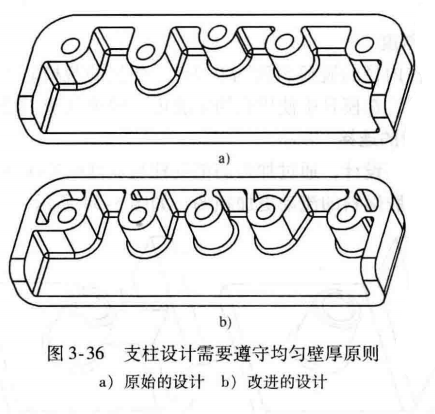
3.5.10 螺钉支柱的标准结构
如果支柱结构是用于自攻螺钉固定,那么这时候的支柱是一个典型的标准特征设计。
作者建议,塑胶支柱的自攻螺钉预制孔需要按照标准来设计,尽量不需要独立“创新”,才能最大可能减少失误。
如下图所示:
后面机械紧固的小章节有详细的推荐数值。
3.6 孔的设计
3.6.1 孔的深度不能太深(若太深,采用阶梯孔成型)
塑胶件的孔、槽以及凹坑是通过模具上的型芯而成型的。型芯是模具上凸起的部分,型芯尺寸影响着模具的寿命和零件的质量等。在零件注射过程中,过高过长的型芯承受着较高的塑胶熔料冲击力,很容易引起型芯的位置移动,从而造成孔槽等尺寸误差大,或者在长期的冲击力之下,型芯容易发生折断而降低使用寿命。因此,塑胶件的孔、槽以及凹坑等相关尺寸设计必须保证合适型芯的尺寸,从而保证模具寿命和提高零件质量等。
塑胶件上常见的孔大致可以分为不通孔、通孔和阶梯孔3种。
当不通孔的直径小于5mm时,孔的深度不应该超过孔直径的2倍;当不通孔的直径大于5mm时,孔的深度不应超过孔直径的3倍。
通孔比不通孔更容易制造,因为型芯可以分布在凸、凹模两侧,通孔的深度可以适当加大。当通孔的直径小于5mm时,孔的深度不应该超过孔直径的4倍;当通孔的直径大于5mm时,孔的深度不超过孔直径的6倍。
不通孔和通孔的深度推荐值如图3-37所示。
如果孔太深,可以用阶梯孔的方法替代成型,如图3-38所示。
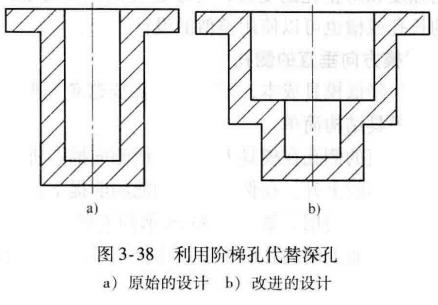
3.6.2 避免盲孔(不通孔)底面太薄
不通孔底部厚度至少应当大于不通孔直径的0.2倍,如图3-39a所示。底部太薄,不通孔强度低,同时背面容易产生外观缺陷。如果底部太薄,则可以考虑使用图3-39b所示的方法增强不通孔的强度。
3.6.3 孔与孔的间距及孔与零件边缘尺寸避免太小
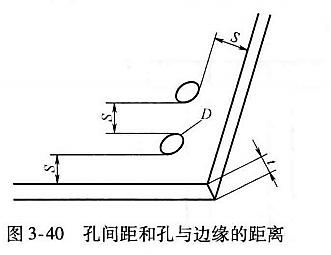
3.6.4 零件上的孔尽量远离零件受载荷部位
由于孔去除了零件的材料,降低了零件的强度;同时孔的周围(特别是有很多孔时)很容易产生熔接痕(见图3-41),零件的强度被进一步降低。塑胶零件常常因为过多的孔而造成强度降低。因此在零件受载荷部位。应尽量避免放置太多的孔。
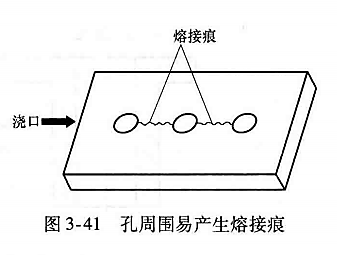
3.6.5 可以在孔的边缘增加凸缘增加孔的强度
为了增加孔的强度和防止孔的变形,可以在孔的四周增加凸缘(见图3-42),对需要增加强度的长孔或槽也可以使用类似的设计。
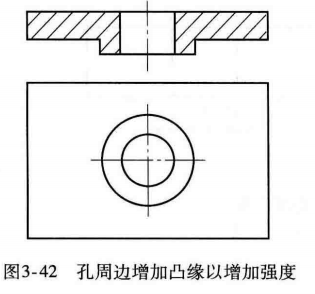
3.6.6 避免与零件脱模方向垂直的侧孔
为简化模具结构,降低模具成本,零件设计需要避免与脱模方向垂直的侧孔。孔的设计应尽量使得模具结构简单。
与零件脱模方向垂直的侧孔在模具上需要使用侧向抽芯机构,这会增加模具的复杂程度,造成模具成本的上升。在保证零件功能的前提下,可以通过设计优化来减少和避免侧向抽芯机构的使用。如图3-43所示的塑胶件,下侧的孔需要侧向抽芯机构,模具结构复杂;而上侧的孔由于设计优化则可以直接脱模,不需要侧向抽芯机构,模具结构简单。
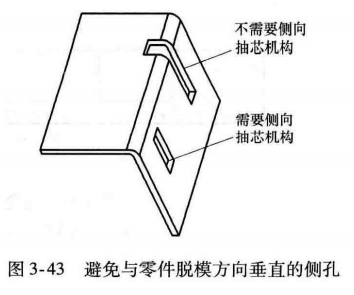
3.6.7 长孔的设计避免阻碍塑胶溶料的流动
长孔是指长而窄的孔。长孔的方向应该与塑胶熔料的流动方向一致,避免垂直于流动方向,以免阻碍塑胶熔料的流动,长孔的设计如图3-44所示。
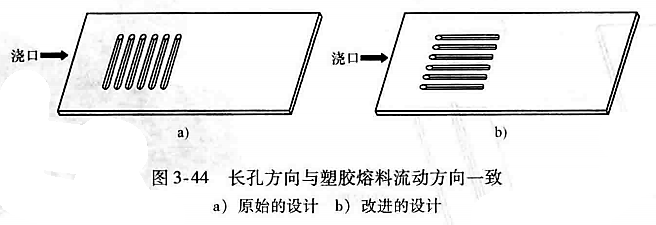
3.6.8 风孔的设计
过多的风孔设计会造成零件强度降低,可以通过增加前几节所述的加强筋或凸缘等方法来增加风孔处零件的强度。
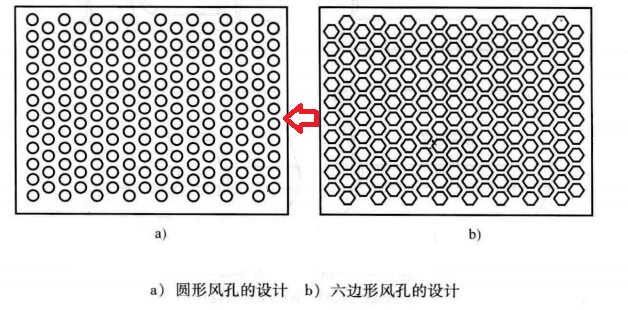
3.7 雕刻文字,符号及花纹
3.7.1 塑胶部品中,超过20g以上的部品,必须追加”材质标识”
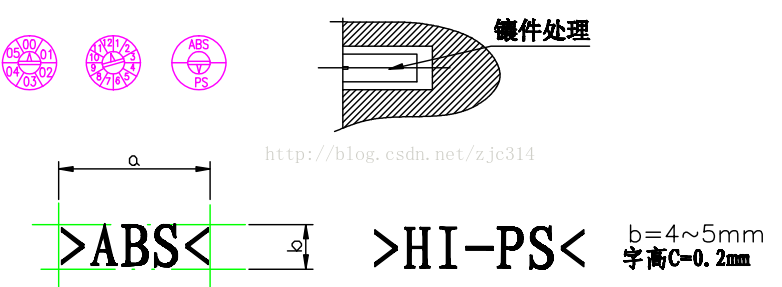
3.7.2 雕刻区通常要求咬薄薄的花纹TH106,目的:避免在塑胶成型时出现流痕.
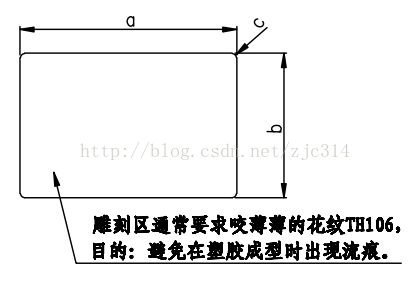
//这个花纹的标准,作者忘记是哪一家的了,暂时也可不做考虑。
3.7.3 零件外观装饰特征及零件上的文字和符号宜向外凸出
零件外观装饰特征及零件上的文字和符号宜向外凸出,模具加工时为下凹,加工容易。
3.7.4 雕刻文字,符号及花纹设计指南
塑胶件上文字、符号的单边脱模斜度取8°~12°。
其余要求需要依据各个行业、公司要求而定。3.8 提高塑胶件强度的设计
塑胶件强度永远是产品设计工程师关心的一个主题。与金属零件相比,塑胶件强度一般比较低,但通过合理的零件设计,塑胶件强度可以大幅度提高,从而可以扩大塑胶件的应用范围。
3.8.1 通过添加加强肋而不是增加壁厚来提高零件强度
零件设计时可以通过增加壁厚的方法来提高零件强度,但这往往是不合理的。零件壁厚增加不仅会增加塑胶件重量,而且容易使零件产生缩水、气泡等缺陷,同时增加注射生产时间,降低生产效率。为提高零件的强度,正确的方法是增加加强筋、而不是增加零件壁厚。増加加强筋既能提髙零件强度,又可以避免零件发生缩水、气泡等缺陷以及生产效率较低等问题。当然,加强筋设计时相关尺寸必须遵循加强筋的设计原则,过厚的加强筋厚度也会造成零件缩水、气泡等缺陷的产生。
两种增加零件强度2倍的方法如图3-45所示。其一是增加壁厚,其二是保持壁厚不变、增加加强筋。为达到零件强度增加2倍的目的,增加零件壁厚的方法需要增加25%的零件体积,而通过增加加强筋的方法仅仅需要增加7%的零件体积。由此可以看出,增加加强筋是提高零件强度最好的方法。
图3-46所示为通过增加加强筋来提高座椅的强度。
//注:加强筋可以减少零件零件整体的变形,但加强筋只要添加就会给零件带来表面的收缩,影响外观。所以真正需要注意零件外观时,可以考虑加厚零件而非加强筋。
3.8.2 加强肋的方向要考虑载荷的方向
需要注意的是,加强筋只能加强塑胶件一个方向的强度。加强筋方向需要考虑载荷方向,否则加强筋不能增加零件抵抗载荷的能力,如图3-47所示。
如果零件承受的载荷是多个方向的载荷或者扭曲载荷,可以考虑增加X形加强筋或者发散形加强筋来提高零件强度,如图3-48所示。在日常生活中,塑胶凳子的背面常是通过X形加强筋或者发散形加强筋来提高零件强度的。
3.8.3 多个加强肋的方向比单个较厚或较高的加强肋好
多个加强筋的设计对零件强度的提髙比单个较厚或较高的加强筋效果好,同时避免了零件表面缩水或者加强筋顶端注射不满等质量问题。因此,当单个加强筋的高度太高或者厚度太厚时,可以用两个较小的不高不厚的加强筋来替代,如图3-49所示。
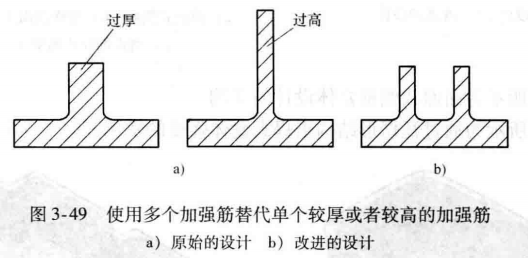
3.8.4 设计零件增强剖面
通过设计零件增强剖面形状可以提高塑胶件的强度,常见的零件增强剖面包括形、锯齿形和圆弧形,如图3-50所示。这种方法的缺点是零件不能提供一个平整的平面,在某些情况下不能使用。
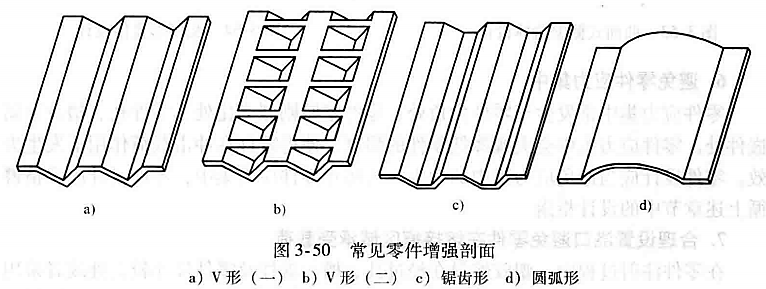
3.8.5 增加侧壁和优化侧壁剖面形状来提高零件强度
避免平面型塑胶件设计,平面型的塑胶件强度非常低,可以通过四周增加侧壁来提高零件的强度,如图3-51所示。
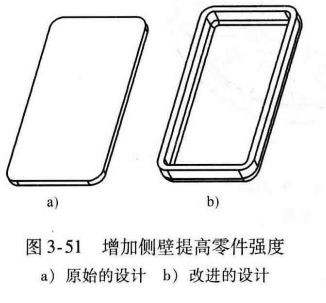
侧壁的形状可以是单纯的直壁,在条件允许时,曲面式侧壁或者带增强剖面式侧壁更能提高零件的强度,如图3-52所示。
图3-53所示为曲面式侧壁盒体设计的实例。
图3-54所示为通过瓦楞形结构来提高盒体强度的实例。
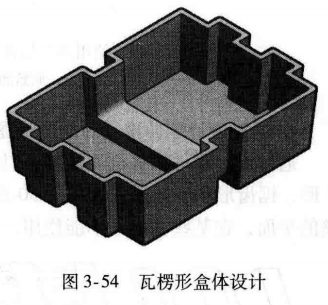
3.8.6 避免零件应力集中
3.8.7 合理设置浇口避免零件在熔接痕区域承受载荷
在零件注射过程中,塑胶熔料在经过孔、槽、支柱及零件尺寸较大处或者采用多个浇口时,塑胶熔料会有两个及两个以上的流动方向,当两个方向的塑胶熔料相遇时,在此区域会产生熔接痕。
零件熔接痕区域是零件强度最低的区域之一,是最容易发生失效的区域之一 。因此必须合理设置浇口的位置和数量,以避免零件在熔接痕区域承受载荷。如图3-55所示,在原始的设计中,浇口的位置使得熔接痕刚好处于零件所受载荷处,零件容易在载荷作用下失效;在改进的设计中,调整浇口的位置,使得熔接痕的位置避开零件所受载荷处,零件的可靠性大大增强。
熔接痕的位置可以通过 Mold Flow等模流分析软件来预测,产品设计工程师可以在零件开模时,要求模具供应商提供零件的模流分析报告,从而合理地选择浇口的位置和数量。
3.8.8 其他强度增强相关因素
1)玻璃纤维增强塑料常用来代替普通塑胶材料来提髙塑胶件强度。需要注意的是,玻璃纤维增强塑胶只在玻璃纤维的方向上提高零件的强度。
2)塑胶件承受压缩载荷的能力比承受拉伸载荷的能力强。
3)在承受拉伸载荷时,设计一致的零件剖面以均匀分散载荷。
4)避免零件承受圆周载荷。零件(如金属嵌件处)承受圆周载荷时,很容易发生破裂而失效。
5)在承受冲击载荷时,保持零件剖面的完整性,避免在冲击载荷方向上零件剖面出现缺口和应力集中。
3.9 提高塑胶件外观质量的设计
在市场竞争日益激烈的今天,产品外观成为吸引消费者购买产品的重要因素之。由于塑胶材料本身以及注射工艺的特性,塑胶件很容易产生缩水、气泡、熔接痕、困气、喷流等外观缺陷,严重影响零件的外观质量。塑胶件发生外观质量冋题主要源于零件设计的问题、模具设计的问题以及零件注射过程中注射工艺参数不正确的问题。对产品设计工程师来说,首先需要从零件设计入手解决零件外观质量问题,特别是当零件是产品外观零件时更应如此,产品内部零件的外观要求则可以适当放宽。
从零件设计的角度上,除了零件设计需要满足上述章节的设计指南外,还可以从以下几个方面来提高塑胶件外观质量。
注:文章把模具设计中浇口的选择和布局、模具通风和模具顶出结构等归结于零件设计,并不是说产品设计工程师需要亲自进行模具设计,而是因为产品设计工程师必须了解模具结构对零件外观质量(或者零件强度)的影响,并检査零件模具结构是否对产品的外观(或者零件强度)产生负面的作用,如果有则要求改进模具的设计,因为模具工程师往往并不知道零件的外观(或者零件强度)的要求。例如,他们可能错误地设计和布局浇口,以至于在产品重要外观面出现熔接痕,此时产品设计工程师就需要指出模具设计的错误并要求改正。
3.9.1 选择合适的塑胶材料
塑胶材料的选取对产品的外观起着重要的作用,不同的塑胶材料有着不同的外观质量表现。例如,相对于非玻璃纤维增强的材料,玻璃纤维增强的材料注射成型后一般外观质量比较低,而且容易翘曲。
3.9.2 避免零件外观表面缩水
零件表面缩水是塑胶件最容易发生的外观缺陷之一。缩水一般发生在零件壁厚较厚处所对应的零件外表面,例如加强筋、支柱与壁的连接处所对应的零件外表面,如图3-56所示。
3.9.2.1 通过设计掩盖缩水
在允许的情况下,可以通过U形槽、零件表面断差的设计以及表面咬花等方式来掩盖塑胶件表面缩水,如图3-57所示。
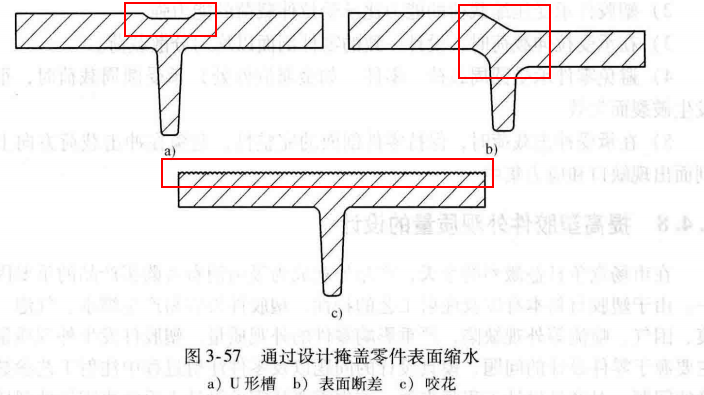
3.9.2.2 “火山口”设计
支柱壁厚处或加强筋壁厚处局部去除材料(我国台湾地区称之为“火山口”),可以大幅降低零件外观缩水的可能性,如图3-58所示。当然,“火山口”设计会在一定程度上降低支柱或加强筋的强度。
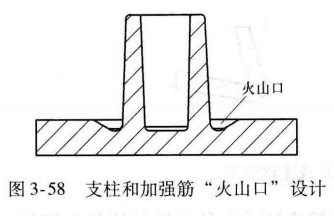
3.9.2.3 合理设置浇口位置
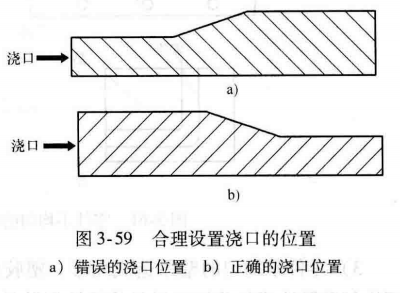
3.9.3 预测零件变形,设计减少变形
零件变形不但会造成零件尺寸精度差,容易产生装配问题和影响零件功能的实现,同时也会影响零件的外观。零件发生变形的原因很多,主要包括4个方面:零件在塑胶熔料流向方向上和横截面方向上不同的收缩比、零件不均匀的冷却、零件壁厚不均匀,以及零件几何形状不对称等。
1)零件在塑胶熔料流向方向上和横截面方向上不同的收缩比。
零件在塑胶熔料流向方向上和横截面方向上不同的收缩比造成了零件的变形,如图3-60所示。
非玻璃纤维增强材料在塑胶熔料流动方向上收缩率比横截面方向上大,造成塑胶在塑胶熔料流动方向上收缩大,在横截面上收缩小,零件发生变形;
而玻璃纤维增强材料则刚好相反,在塑胶熔料流动方向上收缩率比横截面方向上小,造成塑胶在塑胶熔料流动方向上收缩小,在横截面上收缩大,零件发生变形。
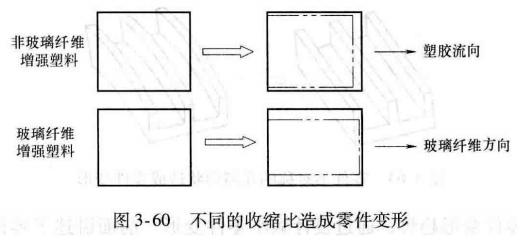
2)零件不均匀地冷却。
零件在壁厚方向上不均匀地冷却会造成零件变形。不均匀地冷却一方面可能是因为注射模具水路设计不均衡造成的,另一方面可能是零件本身外侧的散热面积大于内侧的散热面积,外侧散热较慢、冷却较慢,而内侧散热较快、冷却较快(见图3-61),零件变形的方向总是朝着较热的零件面。
3)零件不均匀的壁厚造成变形。
塑胶件收缩率随着零件壁厚的增加而增加,不均匀壁厚造成的收缩差异是热塑性塑胶件发生变形的主要原因之一。具体地说,塑胶件剖面壁厚的变化通常会引起冷却速率差异与结晶度差异,结果造成零件收缩差异与零件变形,如图3-62所示。
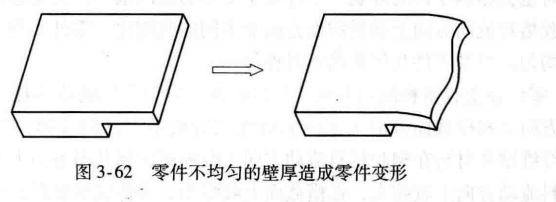
4)零件不对称的几何形状造成零件变形。
零件不对称的几何形状会导致冷却不均匀和收缩差异,造成零件变形,如图3-63所示。
5)预测零件变形趋势,通过设计减小零件变形。
前面讲述了零件变形的原因和方式,但这不是重点,产品设计的重点是预测零件的变形趋势并通过零件设计优化减少甚至避免零件变形的发生,如图3-64、图3-65所示。
3.9.4 外观零件之间设计美工沟
两个外观塑胶件之间配合时,因为零件制造误差和装配误差的存在,两个零件之间的间隙和断差(指一个零件的表面高于另外一个零件的表面)总是会存在的这会影响产品的外观,如图3-66a所示。
通过美工沟的设计可以掩盖两个外观塑胶件之间的间隙,从而提高产品的外观质量。常用的美工沟的设计有两种,如图3-66b和3-66c所示。
美工沟的大小根据产品的尺寸而定,如电脑主机面板美工沟的大小为0.5mm×0.5mm。在两种美工沟设计中,第二种方法优于第一种。第一种美工沟的设计因为间隙的存在使得消费者有可能看到产品内部零件,同时没有防尘的作用。当两个外观塑胶件之间的关系是前后或上下关系时,例如手机的上下盖,此时断差成为影响零件外观的一个因素。如果后面/下面的零件高于前面/上面的零件时,产品就会变得非常难看,因此在这种情况下美工沟设计时应当设计后面/下面的零件低于前面/上面的零件。
3.9.5 避免外观零件表面出现熔接痕
熔接痕也是常见的塑胶件表面外观缺陷,需要避免。具体方法如下:
1)塑胶件表面咬花可以部分掩盖熔接痕,但并不能完全掩盖熔接痕。
2)喷漆可以掩盖熔接痕。
3)合理设置浇口的位置和数量,避免在零件重要外观表面产生熔接痕。
4)保证模具通风顺畅。
3.9.6 合理选择分模线避免零件重要外观面出现断差或者毛边
3.9.7 顶针避免设计在零件重要外观面
3.10 降低塑胶件成本的设计
3.10.1 设计多功能的零件
注射模具通常比较昂贵,设计多功能的塑胶件,能够分担模具成本,从而降低零件开发成本;同时,由于塑胶件可以具有复杂形状和内部结构,一个塑胶件往往可以替代两个甚至多个传统工艺方法加工的零件,而多个塑胶件在有些时候也可以合并成一个塑胶件以节省成本。
例如,在电子电器产品中,合理的电缆线走向和固定对产品的散热和电磁干扰等至关重要。电缆线固定一般通过专用的束线带或线夹来完成,而在塑胶件中增加一些简单的特征即可实现电缆线的固定,如图3-67所示,从而减少束线带或线夹的使用。
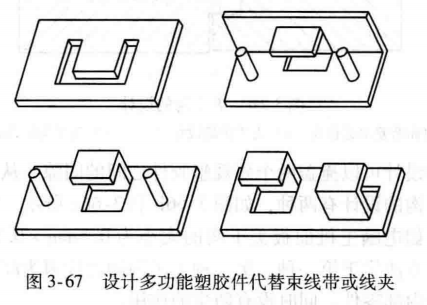
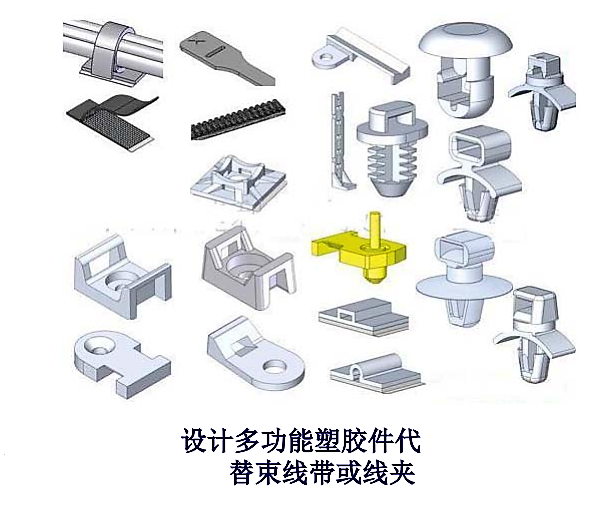
3.10.2 降低零件材料成本
塑胶材料是石油工业的产品之一。随着石油资源储备的不断减少,塑胶材料的价格也在不断上涨。在前几年石油价格飙升的时候,塑胶材料价格的飙升甚至造成中国家电企业不得不提高家电产品的价格。
因此,在保证产品功能等的要求下,零件设计应尽可能使用较少的材料。较少的材料能够降低零件成本,同时避免零件注射时增加注射时间,从而增加注射成本。在减少零件材料的使用时,需要注意:
1)通过增加加强筋而不是增加壁厚的方法来提高零件的强度。
2)零件较厚的部分去除材料。
3.10.3 简化零件设计,降低模具成本
在面向装配的设计(DFA)章节中讨论过KISS原则,KISS原则也适用于单个零件的设计,塑胶件的设计也是越简单越好。复杂的塑胶件形状和结构不但会增加模具结构的复杂性,增加模具的成本,同时会影响零件的质量和性能。
塑胶件应尽可能地设计成多功能的零件,但多功能的零件并不意味着复杂的零件。如果塑胶件多功能的设计反而造成了产品整体成本的上升,这恰恰违反了塑胶件多功能的目的,因为塑胶件多功能的目的之一就是降低产品成本。
3.10.4 避免零件严格的公差
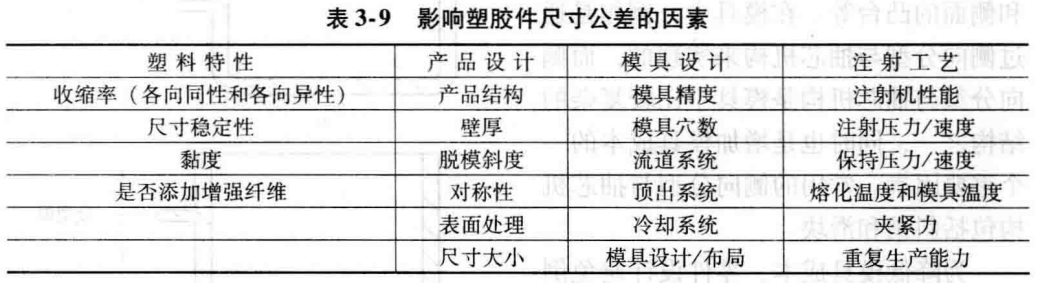
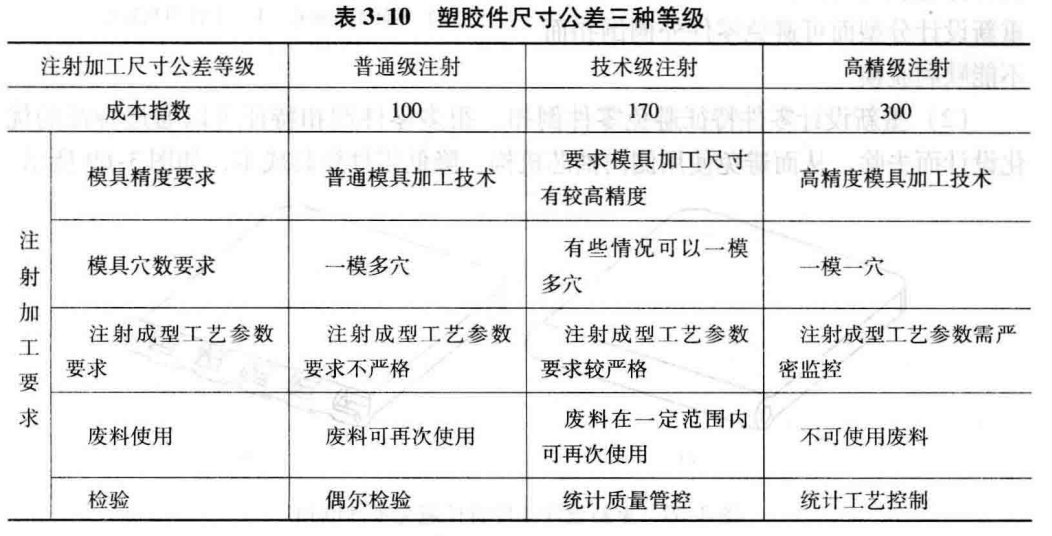
可以看出,塑胶件尺寸公差越严格,对模具精度、模具穴数、注射成型工艺、检验等要求就更高,塑胶件成本就越高。产品设计工程师应当意识到严格的塑胶件尺寸公差对塑胶件零件成本和模具成本的巨大影响。因此,在产品设计时,在保证零件功能等前提下,通过优化的产品设计,尽量避免使用严格的塑胶件尺寸公差。
除了在公差分析红章节中提到的一些公用措施外,对于塑胶件,还有一些措施包括:
①在尺寸精度要求较高的应用场合,选择收缩率低的塑料。
②模具型腔与嵌件、斜销和滑块等配合处存在着额外的对齐误差,避免在该区域提出严格的公差要求。
③预测塑胶件翘曲变形区域,避免在该区域提出严格的公差要求;通常可通过增加加强筋等方式来降低翘曲变形。
3.10.5 零件设计避免倒扣
倒扣是指零件无法正常脱模的特征,例如位于模具开模方向上侧的开口和侧面的凸台等。在模具中,倒扣是通过侧向分型与抽芯机构来实现的,而侧向分型与抽芯机构是模具中比较复杂的结构之一,同时也是增加模具成本的个重要因素。常用的侧向分型与抽芯机构包括斜销和滑块。
为降低模具成本,零件设计避免倒扣是一个重要的手段。
(1)有些外侧倒扣可以通过重新设计分型面来避免
如图3-68所示,重新设计分型面可避免零件外侧倒扣而不能顺利脱模。
(2)重新设计零件特征避免零件倒扣
很多零件倒扣特征可以通过特征的优化设计而去除,从而避免使用侧向抽芯机构,降低零件模具成本,如图3-69所示
如图3-70所示,原始的设计中,零件存在倒扣,需要通过斜销或滑块等侧向抽芯结构来脱模;通过零件特征的重新设计,可以避免使用侧向抽芯机构,在改进的设计中提供了四种方法,见图3-70b、c、d和e。
3.10.6 降低模具修改成本
当一副塑胶件注射模具制造完成后,再进行模具修改的成本非常高,不正确的塑胶件设计往往会增加模具修改次数,提高模具成本,从而增加零件和产品的成本。因此,塑胶件的设计需要尽量减少甚至避免模具的修改。
3.10.6 .1 零件的可注射性设计
塑胶件设计的时候应当充分考虑零件的可注射性。零件可注射性好,零件注射成型后质量高,模具修改次数就少,模具修改费低。如果塑胶件设计不考虑零件的可注射性,零件可注射性差,零件注射成型后质量低,模具修改次数多,模具修改费用就高。因此,塑胶件设计必须遵循本章所涉及的塑胶件设计指南。
3.10.6.2 减少产品设计修改次数
当然,模具修改还可能是因为塑胶件在整个产品中不能实现其应有的功能,因此在模具开发之前,产品设计工程师需要通过CAE分析和运动仿真、样品制作等手段来完善和优化零件的设计,确保零件设计万无一失后,再进行模具的设计和开发,从而减少模具制造完成后的产品设计修改。
3.10.6.3 避免添加材料的模具修改
3.10.7 使用卡勾代替螺丝等固定结构
3.10.8 合理选择模具穴数和冷/热流道系统
模具穴数影响塑胶零件的加工效率。模具穴数越多,模具越复杂,但塑胶件的加工效率越高,加工成本就越低,同时单个零件分摊的流道材料越低。在预期的塑胶件产能要求情况下,通过计算塑胶件成本(材料成本、模具成本分摊和加工成本),可合理选取模具穴数。
另外,合理选择流道系统也有助于降低塑胶件成本。传统的冷流道系统存在着流道材料耗损的缺点,特别是对于昂贵的塑胶材料。而热流道系统则基本不存在流道材料耗损,而且由于没有流道系统,塑件的冷却时间和模具的开模行程都可缩短,从而可以缩短成型周期,另外无须修剪浇口及回收加工浇道等工序,有利于生产自动化;但其缺点是价格较传统的冷流道模具贵。
3.10.9 其他
1)设计零件和模具使得浇口能够自动切除,或者把浇口隐藏在产品内部,避免对浇口的二次加工。
2)把分型面隐藏在产品内部,避免对分型面的二次切除加工。
3.11 脱模斜度
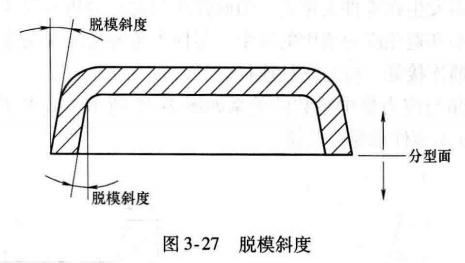
1)零件若无特殊需求,脱模斜度一般取1°~2°;
3d建模时,除非是有重要的设计要求,零件一般不会去特别绘制脱模斜度。但模具设计后开模前,模具审核时需要注意零件内外的脱模斜度是否合理。
2)对于收缩率大的塑胶件应选用较大的脱模斜度。
3)尺寸精度要求高的零件特征处应选用较小的脱模斜度。
4)凸模侧脱模斜度一般小于凹模侧脱模斜度,以利于零件脱模。
5)塑胶件壁厚较厚时,成型收缩增大,因此脱模斜度应取较大值。
6)咬花面和复杂面脱模斜度应取较大值,咬花的大小决定脱模斜度的大小。
7)对于玻璃纤维增强塑料,脱模斜度宜取较大值。
8)脱模斜度的大小与方向不能影响产品的功能实现。
例如,两个零件具有运动关系时,需要考虑配合处的脱模斜度大小和方向,否则会影响产品功能实现。某电器产品上按钮与面板的结构剖面图如图3-28所示,按钮的功能是触发电器开关。
产品设计要求按钮在运动过程中不会被面板卡住,否则按钮不能触发开关,以至于不能正确行使功能,同时要求按钮在运动过程中不会左右摇晃,手感好。这就要求按钮的运动路线是垂直的直线运动,按钮与面板的配合面处必须保证上下间隙致。在原始的设计中,因为面板脱模斜度方向的错误,按钮与面板配合面处上侧间隙大、下侧间隙小,按钮在运动方向上始终只是依靠很小的一个平面与面板接触导向,于是按钮在按动过程中会摇摇晃晃,严重时会使得按钮卡在面板中造成按钮不能触发开关;在改进的设计中,面板脱模斜度方向修改,按钮与面板配合面处上侧和下侧间隙始终一致,按钮的运动路线是垂直的直线运动,按钮手感好,也不会发生按钮被面板卡住而失效的状况。
9)零件某些平面因为功能需要可以不设置脱模斜度,但模具则需设计侧抽芯结构,模具结构复杂,成本高。
10)在零件功能和外观等允许情况下,零件脱模斜度应尽可能大。
较小的脱模斜度会增加零件在顶出过程中表面划伤及损坏的可能性;同时,较小的脱模斜度要求模具表面抛光处理或复杂的模具顶出机构,增加模具成本。
4.注塑件的装配
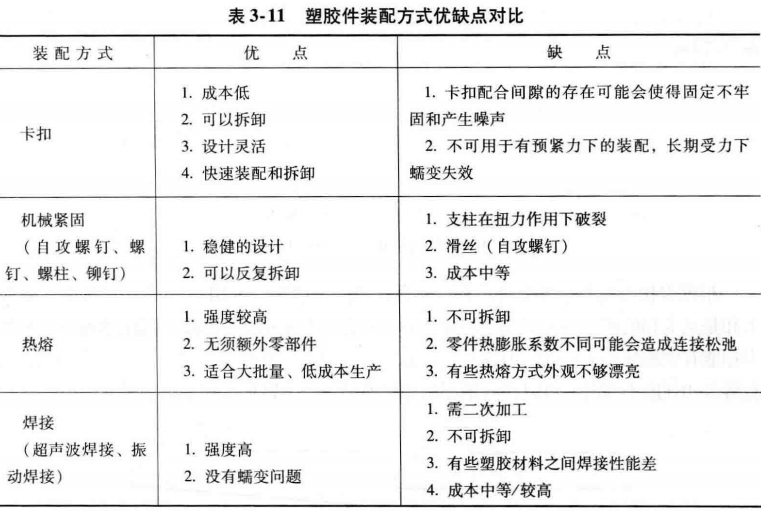
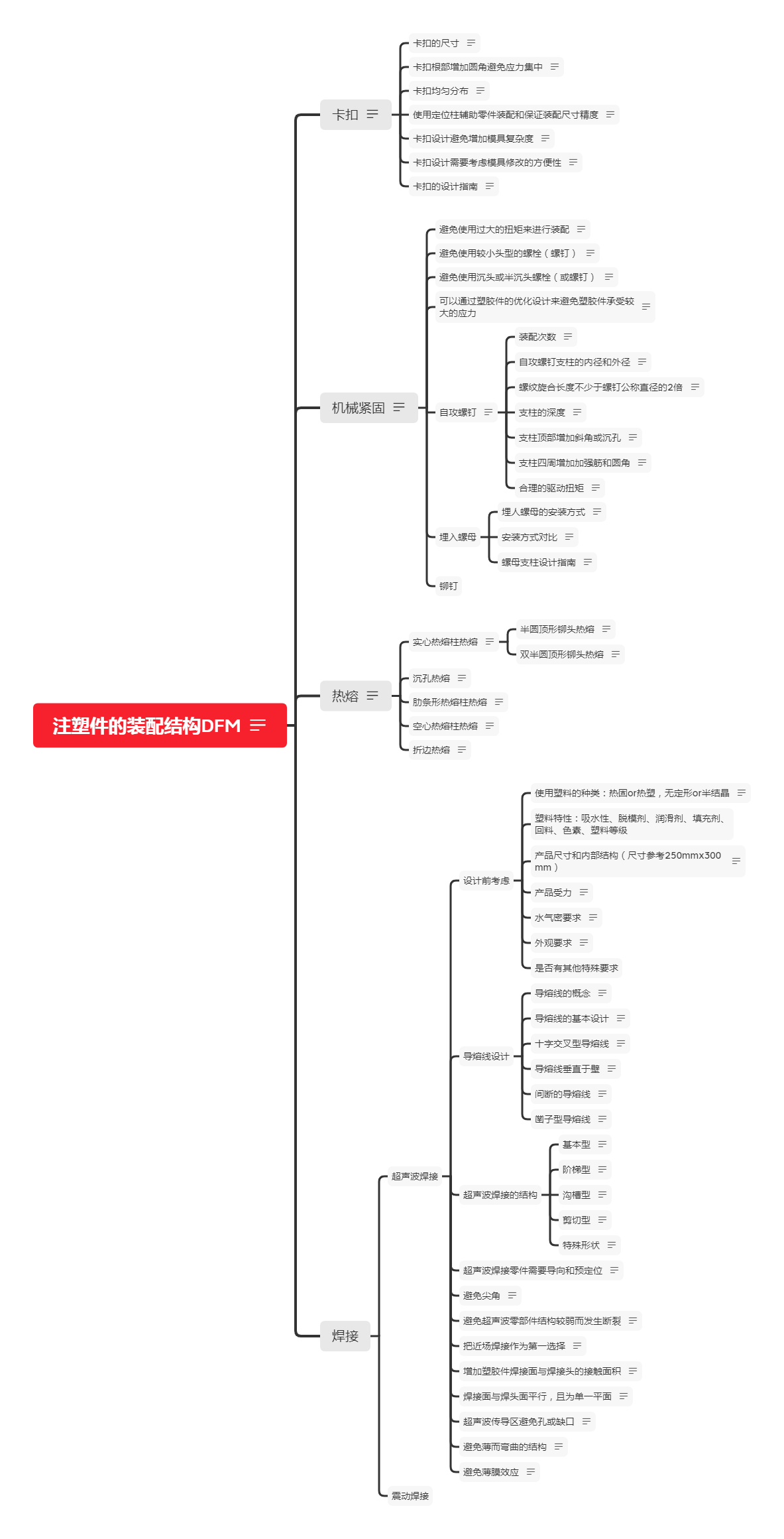
5.注塑件DFMA表格
DFMA学以致用,事前遵循,事后补缺。
5.1 注塑件设计检查
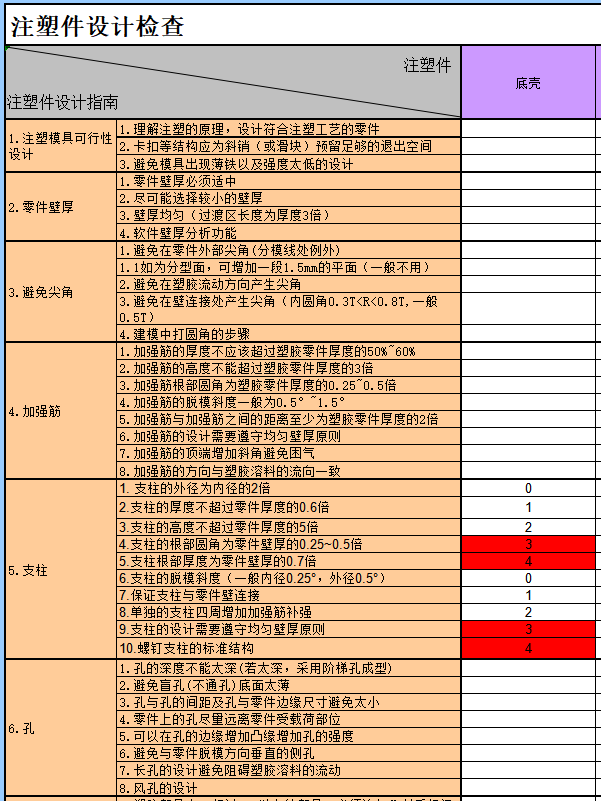
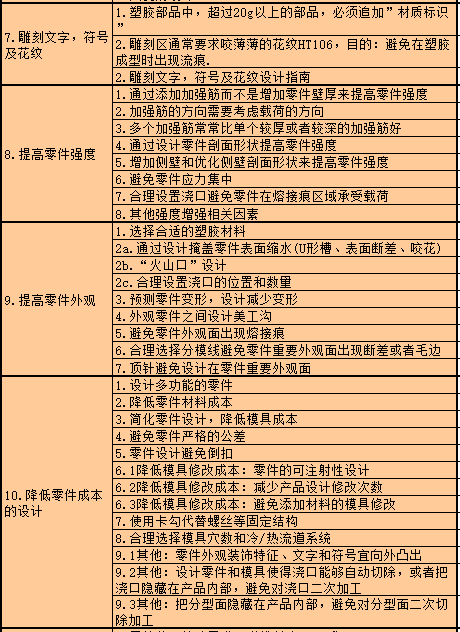
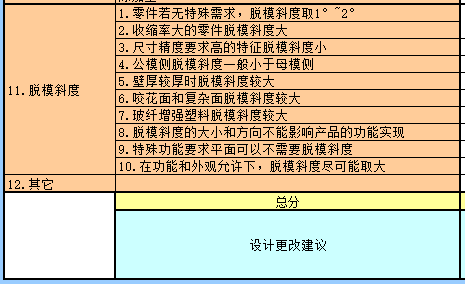
5.2 注塑件装配方式设计检查
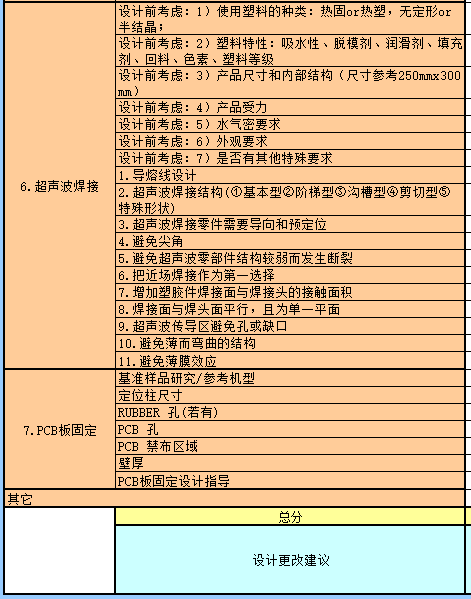
6.注塑件公差标准
6.1 尺寸公差
GBT14486-2008 塑料模塑件尺寸公差;
//有一个不推荐的做法:一般塑胶件最精密的公差要求取±0.05(50±0.05就是塑胶件现有的最好制造能力了),次一等精密的公差取±0.1,不重要的公差可以看用标准取值。
6.2 角度公差
塑胶产品未注角度也可以参考《A324140 塑料件未注尺寸公差》,如下图:
其值等同于GB/T1804-c和GB/T1804-m;
一般塑胶件角度为±1°,极少数精密要求需要控制到±0.5°;
//这是作者统计一家德国公司的多张图纸得出的结论。
//角度的公差判定依据一般是以成型角度两条边的短边长度。短边长度越小,公差越大。而不是角度越大,公差越大。
6.3 形位公差
标准 A32 2100 ,但这份标准作者一直没有找到。
在标注形位公差时,可以用线性尺寸的公差带大小做参考。
6.4 表面粗糙度
《GB/T 14234-93 塑料件表面粗糙度》。
a)蚀纹表面不能标注的粗糙度。在塑胶表面光洁度特别高的地方,将此范围圈出标注表面状态为镜面。
b)塑胶零件的表面一般平滑,光亮,表面粗糙度一般为Ra2.5〜0.2um。
c)塑胶的表面粗糙度,主要取决于模具型腔表面的粗糙度,模具表面的粗糙度要求比塑胶零件的表面粗糙度高一到二级。用超声波、电解抛光模具表面能达到Ra0.05。
具体每种塑胶产品表面要求所具有的表面粗糙度应根据实际情况和客户的要求,对于模具型腔表面要求达到相应的表面粗糙度。
7.注塑件表面蚀纹样板
Mold-Tech蚀纹样板(这家公司的蚀纹是最广泛和全面的)
蚀纹号 |
深 度(英寸) |
最小脱 模斜度 |
蚀纹号 |
深 度(英寸) |
最小脱 模斜度 |
蚀纹号 |
深 度(英寸) |
最小脱 模斜度 |
蚀纹号 |
深 度(英寸) |
最小脱 模斜度 |
MT-11000 |
0.0004″ |
1° |
MT-11200 |
0.003″ |
4.5° |
MT-11300 |
0.0025″ |
3.5° |
MT-11400 |
0.002″ |
3° |
MT-11010 |
0.001″ |
1.5° |
MT-11205 |
0.0025″ |
4° |
MT-11305 |
0.005″ |
7.5° |
MT-11405 |
0.0025″ |
4° |
MT-11020 |
0.0015″ |
2.5° |
MT-11210 |
0.0035″ |
5.5° |
MT-11310 |
0.005″ |
7.5° |
MT-11410 |
0.0035″ |
5.5° |
MT-11030 |
0.002″ |
3° |
MT-11215 |
0.0045″ |
6.5° |
MT-11315 |
0.001″ |
1.5° |
MT-11415 |
0.002″ |
3° |
MT-11040 |
0.003″ |
4.5° |
MT-11220 |
0.005″ |
7.5° |
MT-11320 |
0.0025″ |
4° |
MT-11420 |
0.0025″ |
4° |
MT-11050 |
0.0045″ |
6.5° |
MT-11225 |
0.0045″ |
6.5° |
MT-11325 |
0.003″ |
4.5° |
MT-11425 |
0.0035″ |
5.5° |
MT-11060 |
0.003″ |
4.5° |
MT-11230 |
0.0025″ |
4° |
MT-11330 |
0.002″ |
3° |
MT-11430 |
0.007″ |
10° |
MT-11070 |
0.003″ |
4.5° |
MT-11235 |
0.004″ |
6° |
MT-11335 |
0.002″ |
3° |
MT-11435 |
0.010″ |
15° |
MT-11080 |
0.002″ |
3° |
MT-11240 |
0.0015″ |
2.5° |
MT-11340 |
0.003″ |
4.5° |
MT-11440 |
0.0005″ |
1.5° |
MT-11090 |
0.0035″ |
5.5° |
MT-11245 |
0.002″ |
3° |
MT-11345 |
0.003″ |
4.5° |
MT-11445 |
0.0015″ |
2.5° |
MT-11100 |
0.006″ |
9° |
MT-11250 |
0.0025″ |
4° |
MT-11350 |
0.0035″ |
5.5° |
MT-11450 |
0.0025″ |
4° |
MT-11110 |
0.0025″ |
4° |
MT-11255 |
0.002″ |
3° |
MT-11355 |
0.0025″ |
4° |
MT-11455 |
0.003″ |
4.5° |
MT-11120 |
0.002″ |
3° |
MT-11260 |
0.004″ |
6° |
MT-11360 |
0.0035″ |
5.5° |
MT-11460 |
0.0035″ |
5.5° |
MT-11130 |
0.0025″ |
4° |
MT-11265 |
0.005″ |
7° |
MT-11365 |
0.0045″ |
7° |
MT-11465 |
0.005″ |
7.5° |
MT-11140 |
0.0025″ |
4° |
MT-11270 |
0.004″ |
6° |
MT-11370 |
0.004″ |
6° |
MT-11470 |
0.002″ |
3° |
MT-11150 |
0.00275″ |
4° |
MT-11275 |
0.0035″ |
5° |
MT-11375 |
0.004″ |
6° |
MT-11475 |
0.002″ |
3° |
MT-11160 |
0.004″ |
6° |
MT-11280 |
0.0055″ |
8° |
MT-11380 |
0.004″ |
6° |
MT-11480 |
0.003″ |
4.5° |
|
|
|
|
|
|
|
|
|
|
|
|
MT 9000 |
|
|
MT 9013 |
|
|
MT 9045 |
|
|
MT 9050 |
|
|
MT 9001 |
|
|
MT 9015 |
|
|
MT 9046 |
|
|
MT 9051 |
|
|
MT 9002 |
|
|
MT 9016 |
|
|
MT 9047 |
|
|
MT 9052 |
|
|
MT 9003 |
|
|
MT 9017 |
|
|
MT 9048 |
|
|
MT 9053 |
|
|
MT 9004 |
|
|
MT 9036 |
|
|
MT 9049 |
|
|
MT 9054 |
|
|
MT 9005 |
|
|
MT 9037 |
|
|
MT 9060 |
|
|
MT 9055 |
|
|
MT 9006 |
|
|
MT 9038 |
|
|
MT 9061 |
|
|
MT 9056 |
|
|
MT 9007 |
|
|
MT 9039 |
|
|
MT 9062 |
|
|
MT 9057 |
|
|
MT 9008 |
|
|
MT 9040 |
|
|
MT 9063 |
|
|
K 5000G |
|
|
MT 9009 |
|
|
MT 9041 |
|
|
K 9000G |
|
|
K 5024G |
|
|
MT 9010 |
|
|
MT 9042 |
|
|
K 9070G |
|
|
K 2400G |
|
|
MT 9011 |
|
|
MT 9043 |
|
|
K 7000G |
|
|
K 1600G |
|
|
MT 9012 |
|
|
MT 9044 |
|
|
K 7050G |
|
|
|
|