高阶篇:4)可靠性设计-总章
本章目的:可靠性设计方法指引章节。
1.引子
古英格兰有一首著名的名谣:“少了一枚铁钉,掉了一只马掌,掉了一只马掌,丢了一匹战马,丢了一匹战马,败了一场战役,败了一场战役,丢了一个国家。”这是发生在英国查理三世的故事。查理准备与里奇蒙德决一死战,查理让一个马夫去给自己的战马钉马掌,铁匠钉到第四个马掌时,差一个钉子,铁匠便偷偷敷衍了事,不久,查理和对方交上了火,大战中忽然一只马掌掉了,国王被掀翻在地,王国随之易主。
当然,一个国家的败亡,可以是以一枚铁钉,也可以是一个金币,一块黑面包,一张白纸等。
这里所学的可靠性设计方法,就是能找出国家灭亡原因,找到那枚铁钉,并消除它的方法!
2.可靠性定义
什么是可靠性?
①所谓的可靠性,是指一个产品在顾客使用的期间,是否能完美达到其预设的菜单表现。可靠性亦称之为持续质量。
②产品、系统在规定的条件下,规定的时间内,完成规定功能的能力称为可靠性。
③可靠度:是用完成规定功能的概率表示。
①为新定义,②为旧定义,③为可靠度,口语中常常和可靠性混淆。
3.可靠性设计定义
学习了可靠性,再明确可靠性设计。
可靠性设计:保证机械及其零部件满足给定的可靠性指标(客户预设的菜单表现)的一种机械设计方法。包括对产品的可靠性进行预计、分配、技术设计、评定等工作。
从可靠性设计的定义可以看出,新可靠性定义的重要性。
3.1 可靠性设计的目的和任务
可靠性设计的目的是:在综合考虑产品的性能、可靠性、费用和设计等因素的基础上,通过采用相应的可靠性设计技术,使产品的寿命周期内符合所规定的可靠性要求。
系统可靠性设计的主要任务是:通过设计,基本实现系统的固有可靠性。说“基本实现”是因为在以后的生产制造过程中还会影响产品固有可靠性。该固有可靠性是系统所能达到的可靠性上限。所有的其他因素(如维修性)只能保证系统的实际可靠性尽可能地接近固有可靠性。
可靠性设计的任务就是实现产品可靠性设计的目的,预测和预防产品所有可能发生的故障。也就是挖掘和确保产品潜在的隐患和薄弱环节,通过设计预防和设计改进,有效地消除隐患和薄弱环节,从而使产品符合规定的可靠性要求。
也可以说可靠性设计一般有两种情况:一种是按照给定的目标要求进行设计,通常用于新产品的研制和开发;另一种是对现有定型产品的薄弱环节,应用可靠性的设计方法加以改进、提高,达到可靠性增长的目的。
3.2 设计的基本原则
在可靠性设计过程中应遵循以下原则:
(1)可靠性设计应有明确的可靠性指标和可靠性评估方案;
//比如fmea的评价系统就是明确的评价指标和方案。
(2)可靠性设计必须贯穿于功能设计的各个环节,在满足基本功能的同时,要全面考虑影响可靠性的各种因素;
(3)应针对故障模式(即系统、部件、元器件故障或失效的表现形式)进行设计,最大限度地消除或控制产品在寿命周期内可能出现的故障(失效)模式;
//可靠性设计的裕度,失效安全设计,防错等。
(4)在设计时,应在继承以往成功经验的基础上,积极采用先进的设计原理和可靠性设计技术。但在采用新技术、新型元器件、新工艺、新材料之前,必须经过试验,并严格论证其对可靠性的影响;
(5)在进行产品可靠性的设计时,应对产品的性能、可靠性、费用、时间等各方面因素进行权衡,以便做出最佳设计方案。
3.3 可靠性设计方法
可靠性设计方法不是唯一的,而且随着时代的进步而变化,系统而详尽的方法是一种趋势。
这里只介绍一套作者所了解、使用和总结的最好的可靠性设计方法,做为分章的引子。
其金字塔的设计顺序分为四部,如下所述:
1)QFDI(顾客需求转换为设计要求);
2)QFDII(设计要求逐层分配给各零件);
3)DFMEA设计失效模式和失效后果分析;
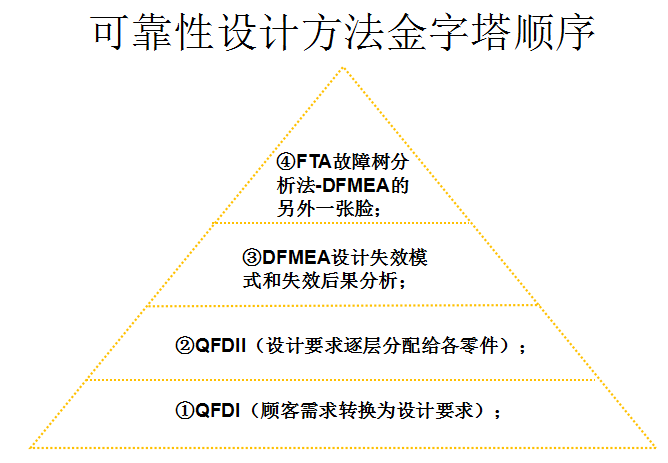
QFDI→QFDII→DFMEA→FTA,切记,莫要乱了顺序,都不是容易的方法,请按部就班的来学习和设计。
4.可靠性设计方法就是投石器
各种可靠性机械设计的准则相当于板砖,可靠性设计方法(QFD、DFMEA)相当于投石器。(这是作者想到的合适的比喻)
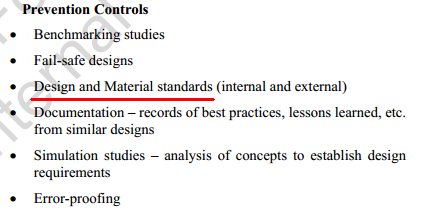
如上图所示,有哪位机械设计工程师不知道按照标准来进行结构设计吗?不可能。
但知道归知道,怎么运用这些设计准则是有区别的!
另外,从作者的实践来看,QFDI→QFDII→DFMEA→FTA,这一套连贯的方法最大的作用的是:有脉络地做可靠性设计。不再会单靠直觉或所谓的经验来发现和解决问题(又不是玩猜谜)。
虽然繁杂,但确是降低了各个步骤的可靠性设计难度。
5.可靠性设计方法的进化对比
就以可靠性的失效后果的严重度(就是出了错会有什么事的程度),为例。
1)以前严重度的标准
这是JB5054标准上的,2000年。
2)现在严重度的标准
这是FMEA手册第四版严重度评价办法,国外2008年。
由此可见,可靠性的设计方法并非一直不变的,随着时代的进步而进步。
5.1 是否评价标准越详细越给结构工程师带来负担?
如题,是否评价标准越详细越给结构工程师带来负担?
作者的回答是,不一定。
一般来说。评价标准越详细,的确可以有利于结构设计的优化,也是今后发展的趋势。如FMEA的RPN升级到AP(第五版)的系统。
但详细的评价如果是用手工或人力来完成,当然会带来严重的负担。反之则未必,如果只是单纯的电脑自动评价,反而是减少负担的一种表现。
就如网络游戏一样,游戏中的攻防血蓝等评价系统,也很复杂,需要ATK,defense,buff,debuff等一堆数值加加减减,但有几个玩家会觉得这些东西是负担了╮(╯▽╰)╭。
6.可靠性设计方法的引入代价
至于这么好的东西,为什么国内设计行业不快快引入呢?
机械行业从来是一分付出,一分收获。质量设计体系(框架)的实施比单纯解决可靠性问题的好很多,付出的也要多很多。
从作者看来,有以下的代价,是必须要付出的。
6.1 认知到质量设计体系的作用。
就拿FMEA举例。
FMEA体系最初是用于航天航空的,20世纪50年代,美国格鲁曼公司开发了FMEA,主要用于飞机制造业和发动机故障评估,取得很好的实效。后来又被应用于汽车行业,1972年,美国福特汽车公司受到美国太空总署许可正式在汽车行业使用FMEA。
可以看出只有对可靠性要求严格的行业,才需要FMEA的体系,国内也只是到车企才需要一些FMEA的要求,而且未必得到重视。但国外的一些家电或消费类电子行业却是早早的采用了它,如Pana*nic和摩托*拉等。
首先,要认知到这个体系针对可靠性设计是有用的,这一点就非常难。
其中重要的一点,就是现在很多厂家的FMEA只是一个失效记录本子,并不能真正起到设计和制造的辅助左右,而且,不完整。这样的体系的确很难让人认识到它的作用。
6.2 质量体系(框架)的搭建
fema体系既然是被比作投石器,其制造难度当然不是板砖可以比拟的。fema体系与可靠性设计表里一体,这个又需要牛人和一堆工程师来通力。
认识到作用,愿意付出代价,并且不是急功近利地做什么事情才找对应的工程师,这是非常困难的。
7.可靠性设计方法资料分享
这套可靠性设计方法是作者搭建产品设计框架的重要的一步。如下图。
实践是比较困难的,可以一步一步来,如FEMA不能做到位,可以先做完整的QFD也行。只有实践,才能明确各种方法的作用。
可靠性设计方法的资料分享在下面网盘中。
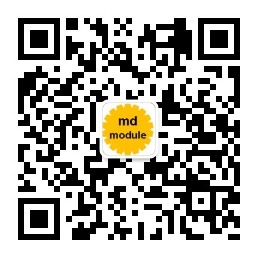
QFD链接:https://pan.baidu.com/s/1P2UH3cJ1FFk-Nafa35043g 密码:b08t
DFMEA链接:https://pan.baidu.com/s/1hgeAibYK9suANs83wnDjfQ 密码:zhz8