APS排产智慧:识别并应对生产中的隐藏风险
APS高级排产软件以其强大的数据分析能力、准确的生产任务计划能力,成为企业在当前环境下进一步提升企业竞争力的有力工具。APS系统综合考虑设备、人力、物料、供应商等多维度因素,通过实时监控生产数据和动态调整产品生产过程顺序,确保建立计划的准确性。定向的数据分析和可视化工具帮助企业深入理解生产数据,发现企业整体生产业务流程的潜在问题,提升生产效率和风险管理能力。
设备资源方面
- APS系统能够根据机器使用效率和维保计划,跳过机器故障时间并提前安排维护,并切换产品加工设备,减少停产时间;APS系统通过产品工序的开工时间和BOM需求,提前安排相应原材料到指定设备,减少浪费并确保生产的连续性和高效性;
- APS系统会根据产品生产任务的实际情况和设备的产能状况,动态调整生产计划,包括优化生产顺序、选择合适的生产设备、平衡各设备的生产负荷等,以确保设备的产能得到充分利用;
- 通过设备采集系统,APS系统能够实时监控设备的运行状态和生产数据,以便及时发现并解决潜在的问题,进一步优化生产计划和排程方案。
人力资源方面
- APS系统根据产品工艺取到各道工序最少加工的单位人力,并在满足最少人力需求的基础上,灵活调配人力资源放大产能,以应对生产过程中的突发情况或变化;
- 为了避免人力资源的浪费以及生产现场的工序工位限制,APS系统会设定每个工序的人力上限,确保在不过度投入人力的同时,保持生产线的稳定性和效率;
- APS系统综合考虑不同产品工序之间的人力需求,确保整个生产过程中的人力资源平衡,实现产能最大化的释放并缩短生产周期。
物料库存监测
- APS系统通过与WMS系统的结合能够实时跟踪物料库存状态,并根据产品工序的物料需求生成产品每道工序的物料需求计划及备料计划,采购部门可以依据数据进行物料采购的下发;
- 对于原料已齐套或即将齐套的产品,APS给予较高的生产优先级,确保生产线不会因缺料而闲置;
- 当某些物料的到货时间发生变化时,APS动态调整生产计划,重新安排生产顺序,以最小化对整体生产进度的影响。
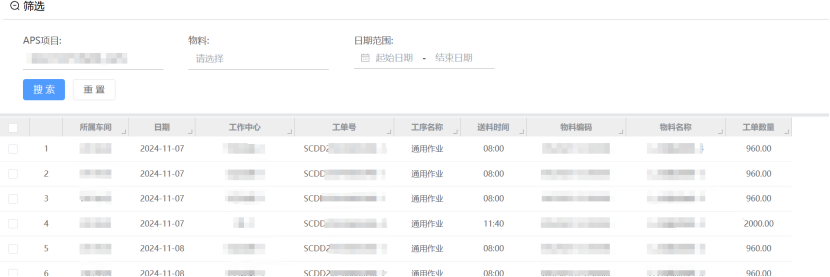
供应商可靠性评估
- 通过在系统内设置供应商的交货方式和策略,APS预测供应商的交货时间和数量,并依据此数据保证产品工序的原料齐套时间足够准确,保证产品加工的稳定性;
- 通过与供应商共享物料需求等信息,APS系统加强与供应链其他环节的协同工作,保障生产顺利进行。
瓶颈工序识别与优化
- APS系统能够自动识别生产过程中的瓶颈工序,通过增加人员、增加每天工作时间、增加设备并行来减少这些瓶颈环节,缩短产品生产周期;
- APS系统分析产品拆分之后的所有加工步骤内的瓶颈,识别出哪些环节是限制整体生产速度的关键因素,并提供瓶颈报表,同时APS系统通过多次迭代排程找到各类瓶颈消减优先级,处理高优先级得瓶颈,使得整体生产周期缩短最大的天数;
实时数据分析和监控
- APS系统通过实时收集生产线、设备状态、物料供应情况等数据实现产品加工过程中的实时监测,能够及时发现生产过程中的异常情况,如设备故障或物料短缺,从而快速响应并调整生产计划;
- 利用深度学习分析历史数据,包括销售记录、市场趋势和产品成交情况,APS系统可以输出一定时间周期内产品需求,帮助企业提前规划生产,在当前产能富裕的情况提前备货,加快产品交付;数据分析功能还提供了各种统计报表和可视化图表,将各类问题进行数字化展示,明确生产过程中的问题所在,并为管理层制定决策提供数据依据;
- APS系统通过与MES系统的集成,对车间生产过程的汇报数据进行采集并进行实时分析,监控产品质量和产品进度是否符合要求。一旦发现大量产品质量问题出现比例超过设置的警戒线,系统可以立即发出警报,并根据历史的处理结果给出相应的预处理方案。
- 通过甘特图,APS系统将生产计划的整体进度和各任务之间的关系进行直观展示,帮助企业更好地把握生产进度和合理分配资源,提高生产计划的质量和执行效率;